Sage 200 - Supporting compliance in food and drink sector
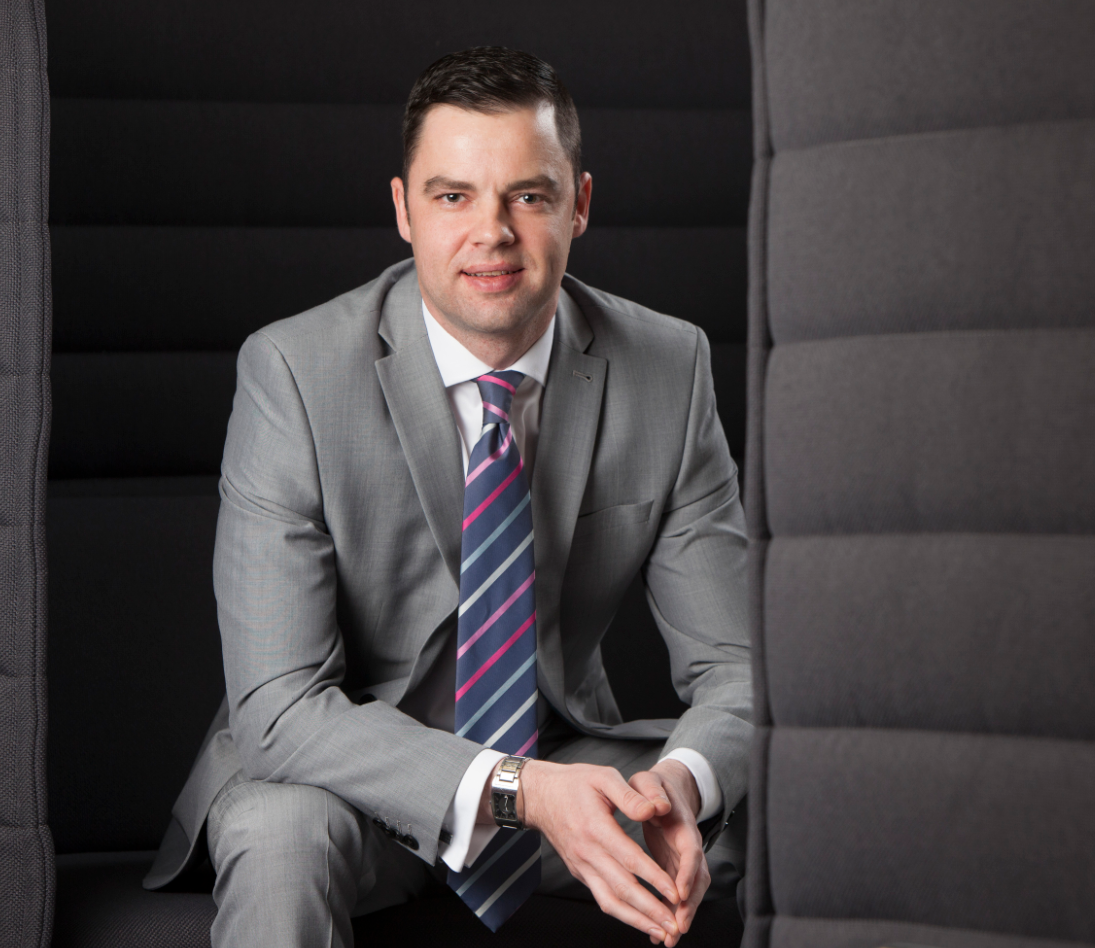
To maintain standards and reduce risk, food and drink companies need to ensure their processes are strictly adhered to, with raw materials and end products alike being stored and used according to the defined manufacturing workflow.
In-built checks and balances within Sage 200 ensure that your teams get it right. It takes on the challenge of managing stock in multiple locations, whether this means in different rack locations or even warehouses on different sites.
Here are some examples:
- Control and management of stock expiry dates best before/used before can be triggered through reporting or works spaces, while Pinnacle Alerts can send out proactive notifications to nominated people
- You have peace of mind that you can perform full batch tracking/date monitoring, ensuring that stock is correctly rotated
- Automatic increment of standard shelf-life through used-by dates by days/weeks/months/years – this can be amended manually at point of entry if required
Trying to do all this on spreadsheets would be incredibly time-consuming and prone to errors and oversights.
Minimising the risk of human error
With Sage 200, you can, for example, assign certain stock codes to specific locations. So, this means in practice that, say, a pie manufacturer can restrict stocks of raw chicken to an area of the warehouse, notional location that they might term the ‘butchery’.
Sage manages the process throughout the production run, so that later the finished pies must be booked into a location for quarantine and inspection before they leave the factory.
This means the uncooked meat is never allowed anywhere near the finished goods – Sage 200 would simply not allow it! – and staff are forced to put the product through inspection.
In other words, while Sage 200 is an incredibly flexible system in accommodating your business processes, it’s unbending where you need it to be. The result: no stage is missed in your workflow is skipped and no materials or products are wrongly assigned.
In an industry that is governed by tight legislation, Sage 200 helps you to get it right, time after time.
Next time
So far, I’ve covered how Sage 200 assists food and drink companies with traceability and process management. In the final blog post, I’ll explain how it helps in managing variable units of measure.
Just add Sage
With over 50 clients in the food and drink sector, Pinnacle can help you to find the optimum Sage solution for your business.
To find out more:
Call 0843 453 0103